The Regalness of Extravagant Mysore Silk
- Lifestyle Medieval history
Khadija Khan
- January 12, 2023
- 0
- 657
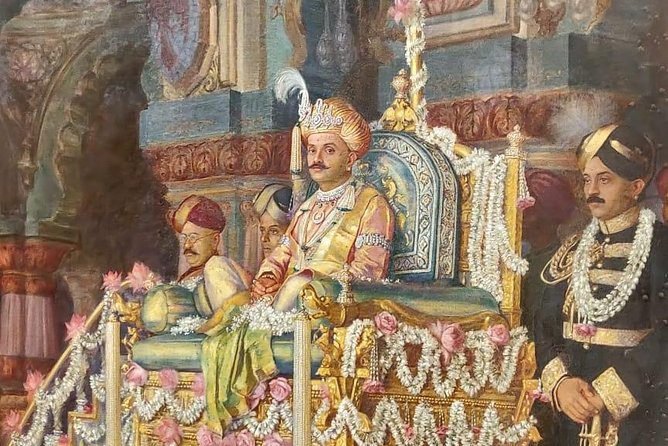
Mysore silk– a fibre with its own stature, that comes from a royal kingdom famous for its fragrant sandalwood oil. Mysore silk sarees have a prestigious past due to its association with South Indian royal history. They are highly sought after for their rich quality and sheen. Indian brides love the silk for its opulent appearance and silky feel. The continuous passion for this silk fabric in the Southern region of the country, where it originated, is mirrored by the rising demand for it in the North.
This fascinating fiber’s history begins during the reign of Tipu Sultan, when the region’s whole new silk industry was sparked by the desire for this particular type of silk. In Mysore, the practise of producing silk grew widespread and one of the most lucrative and well-liked civilizations of the time.
The 20th century saw a major resurgence in the production of this silk as the fashion for Mysore silk sarees and its gold and silver mixed zari prompted many people to admire and copy the well-known South Indian clothing. Another intriguing aspect is that even after being worn for several years, the colour and lustre of the zaris do not fade, making these sarees easy to keep.
The Maharajas and Sultans were so enamoured with the shimmering Mysore silk that they decided to cover everything with it. The weavers’ special skill and the elaborate Mysore silk saree patterns favoured by South Indian royalty attracted equal attention. Because of the infatuation with silk, production increased despite the kingdoms’ ongoing conflicts.
The Wodeyar Maharajas supported silk production, paving the stage for the establishment of India’s first silk manufacturing facility. Karnataka Silk Industries Corporation (KSIC) is currently in charge of this plant, which is powered by 32 power looms imported from Switzerland and used to weave what are now known as Mysore silk sarees.
Techniques involved:
- Soaking:
Because it softens the cloth, coconut oil is used to temporarily colour it.
Temporary colour is used to distinguish between the warps and wefts.
Aluminum tubs are filled with steam from the boiler house.
Raw silk yarn is divided into warp and weft according to the manufacturing schedule.
- Warping/Twisting:
The concentrated solution is transferred to a plastic container and diluted it to the necessary strength.
The silk is rinsed, coloured as needed, hand squeezed, and hydro extracted.
Dressed and air-dried in the shade.
Material moved to shops for soaking silk yarn once it has dried entirely.
- Wefting:
Water is boiled and and 2% to 3.5% soap is added on the weight of material and the soap is allowed to melt completely. 6% to 8% coconut oil is added too and boiled till the coconut oil emulsifies completely. The solution is divided into two equal parts and “Blue” color tint is added for “S” direction and the solution I added to required level and the silk is steeped for approximately 3 to 4 hours.
“Orange” color tint is added for “Z” directions.
The material is hand squeezed and dressed and dried in shade.
Both orange colored and Blue colors are dressed separately. After completely drying, the material is shifted to soaked silk yarn stores lot wise.
- Dressing:
The semi-dry silk bundles are tied to form a circle and are hung on GI pipes until they become completely dry.
- Weft Section:
Doubling:
The silk thread is doubled by running two threads at once from two different bobbins onto a single bobbin and passed onto twisting. The machines have rubber rollers to provide tension while twisting.
Twisting:
Doubled weft threads are twisted here.
The blue tinted threads are given an ‘S’ Twist in the clockwise direction.
The orange tinted threads are given an ‘Z’ Twist in the anti-clockwise direction.
The thread from the bobbins is now wound around a barrel and perforated hollow aluminum pipes.
Steam enters on the insides and spreads the temporary color equally.
Barrels from 3 out of 4 such machines are placed for a period of 40 minutes for steaming
1800 twists are made at this stage and they are now transferred to bobbins which move onto the pirn winding section under the weaving section.
Pirn Winding:
This section consists of 12 machines of 6 pirns each which transfer the thread from the bobbins onto the pirns that fit into the shuttles for weaving, done only for the wefts.
- Warp Section:
The winding process is the same for both the making of the warps and the wefts.
Cone Winding:
A single cone consists of silk generated through 80-90 cocoons, and it akes hours to wind one cone. The machine threads 162 meters of silk onto one cone in 1 minute so evenly that when it goes to the weaving section there are no gaps found in 14,800 silk threads wound around one cone.
Warping Machine:
All the cone bobbins are transferred on a semi-automatic warping machines and mounted on sponge discs to prevent erosion of silk threads which run over into a perforated structure before the warp rolling machine.
The silk threads from each bobbin make a net like structure and before passing through the perforations, the machine indicates an error sometimes caused by a loose or cut.
The skilled artisans identify immediately and fix it. These threads then pass through minutely spaced steel structures, under a roller and a knot is made to mark one section of the silk threads. At every 900 meters of silk thread, a cut is made and 51/2 meters in length. The saree is made into rolls.
- Gold lace section:
The gold and silver is imported from Surat. It consists of around 65% gold and 65% silver.
Gold Warping:
For warping, gold threads from the bobbins are transferred into rolls. Small versions of the warp machines and shuttles are used in the weaving.
Gold Wefting:
All three materials are wound into one bobbin which is later converted into a pirn to fit into the shuttle for the weft.
- Weaving process:
The looms are supplied with patterns by the design section. These patterns are fed into the machine to weave designs onto the sarees.
The power looms are of two types:
Jacquard looms:
These looms are powerful and require years of experience for the labourers to be able to handle them. The patterns are repeated and need to be monitored to see if any thread gets cut or loosens. Each saree takes about 4 hours on the machine to make big borders of gold on both sides of the saree.
Dobby looms:
This is a type of floor loom that controls the whole warp thread by using a device called dobby. Every warp thread on the loom is attached to a single shaft by a device called heddle. A manual dobby uses a chain of bars, each of which has pegs inserted to select the shafts. Computer assisted dobby uses a set of solenoids or other electric devices instead.
- Degumming:
The degumming process is done to smooth the fabric before dyeing and this section consists of 4 tanks. round 230 sarees are clamped by metal springs and are soaked in the solution of soap chips and soda ash for 2 hours. The sarees are then levered out through a semi-automatic machine and are put in hot water again for 15 minutes.
Machines called winches then help in the colouring of the sarees. The tank is connected to a colour tank through a pipe. The colour is in the form of a liquid and is determined from its shade. During the colouring the sarees that were stitched together are manually taken out. The coloured sarees are clamped and covered in plastic bags and the border is left exposed. The border is then dipped in water at 120⁰C and the colour is added. The sarees are then washed with water to remove excess colour and eventually sent for hydro-extraction.
Other varieties of silk saree lack the gloss and brilliance of Mysore silk sarees. These sarees are uniquely created, in contrast to other fake silk fabrics that are mass-produced, which is an intriguing truth about them. Because each work is unique, its durability and individuality are guaranteed. More than the glazing, it is the elegance and simplicity that give it its unique character and give its look and feel a polished air.
The colour consistency of genuine pieces allows for easy identification. These silk sarees have zaris and gold-threaded borders, and they are all one colour. Some sarees also contain exquisitely crafted floral motifs and finely done patterns of mango buttis to add to the appearance. These sarees are made with Kasuti embroidery and Bandhani patterns.
Traditional Mysore silk clothing is not overly bulky. However, crepe and georgette are always options for women who love light Mysore silk sarees. These sarees may be worn for informal occasions, which makes them an ideal addition to many women’s daily wardrobes. Although one can choose mild hues like beige, elephant grey, coffee brown, etc., most of these sarees come in vibrant colours to match the skin tone.
Although some purchasers are dubious about genuineness and hunt for techniques to examine and recognise pure silk, Mysore silk KSIC sarees are genuine. Natural silk is more environmentally friendly than the artificial silk produced on industrial looms.
A quick “Burning Test” may be used to identify genuine silk at any time and anyplace. Both the warp and the weft of pure Mysore silk sarees are created from pure silk threads. It is possible to tell if the silk being used is authentic by burning a little bit of thread in both directions. Pure silk burns like hair and produces a black residue that may be crushed to powder by pressing it between fingers.
These sarees are appealing for both occasional and casual wear. For traditional occasions like religious rituals, weddings, and festivals, sarees with a lot of embroidery and ornamentation are chosen. The luxury and weight of the intricate motifs and embellishments worked together to create a melancholy appearance. However, one may select the perfect lighter and more delicate variants. However, one may choose the more delicate and light variations, which are perfect for social events and celebrity parties. Depending on the decision and the circumstance, one can wear any colour or style.